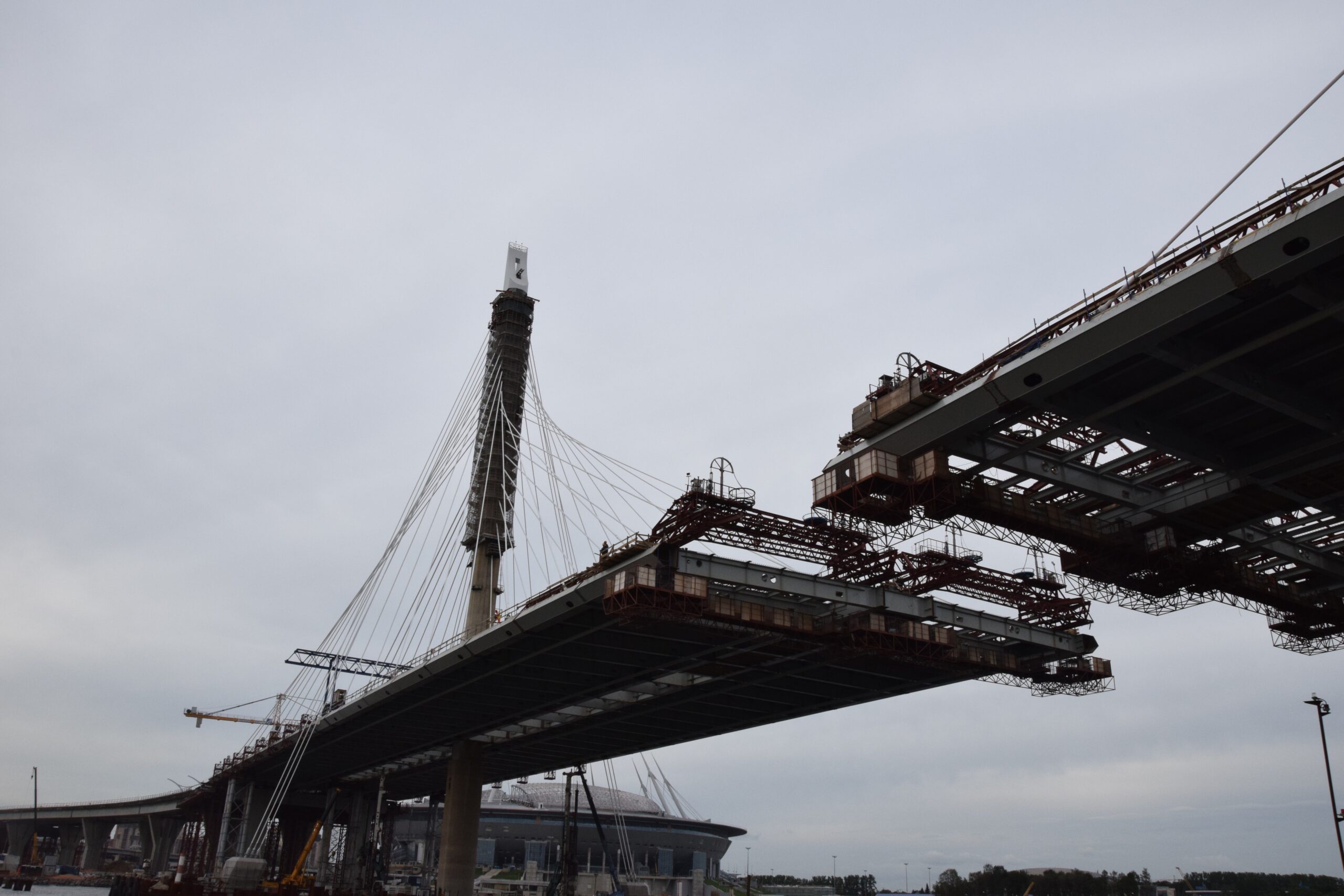
Long ago, but not long forgotten, Australia experienced its worst industrial accident – the 1970 collapse of the West Gate Bridge. Two years into the construction of Australia’s second largest bridge (at the time), a 2,000-tonne section of the steel box girder structure fell to the ground and into the water below, killing thirty-five construction workers and engineers. An 80-day Royal Commission attributed the failure to the design and construction methods. This tragedy serves as a stark reminder of the high-risk nature of bridge construction and why it is important to get it right.
Design and Construction Risks
Few construction projects are realised without complexity and risk, and bridge projects are no exception. Incumbent on each contracting party are the requirements to analyse the risk profile, allocate and assume responsibility, and deploy effective processes to manage those risks throughout the life of the project. In addition to a worst-case scenario such as the West Gate Bridge tragedy, the failure to address the inherent risks of a bridge project prior to, and after, entering into a contract can lead to unfavourable assumption of risk, disputes between the parties, and increased costs and delays.
Common design and construction flaws that may contribute to bridge failures include:
- failure to account for shear stress and strain in soil;
- failure to account for soil subsidence and settlement;
- scour;
- incorrect selection of materials;
- failure of bridge components and connections;
- structural weaknesses;
- inadequate testing; and
- designs failing to account for potential project variables.
Contractual Risk Allocation
As bridge projects in Australia increase in size and complexity, so too does the opportunity for error. Therefore, it is critical for contracting parties to identify and manage the risks involved to meet the project objectives, ensuring successful completion without delay or additional costs. This can be particularly important during the procurement phase, as a failure at this stage to correctly diagnose project risks can result in significant time delays and costs during the construction phase. Common traditional contracting options available to parties for bridge projects include:
- Construct only;
- Design and Construct (D&C);
- Design, Construct and Maintain (DCM); and
- Engineering, Procurement and Construct (EPC).
These options are often preferred by Principals for their simple approach to making certain the risk profile and alleviating risk through allocation to other participants along the procurement chain.
Collaborative Contracting in Bridge Projects
More recently, collaborative contracts have become more commonplace in high-value projects, as principals’ endeavour to align parties’ commercial interests during the contracting stage. Collaborative options to contracting include target-cost, alliancing and partnering agreements.
Collaborative contracting models can facilitate a more streamlined approach to project risks where parties work cooperatively and collaboratively to address issues as they arise. These models may also help foster mutually beneficial relationships between parties, and financially motivate contractors to act in the best interests of the project.
Notwithstanding the collaborative principles of a contract, where a matter descends into dispute, it can present issues where parties are faced with either continuing to act in a collaborative and cooperative manner, or engaging in a blame game about who is at fault. Where parties view the blame game to be more beneficial in overcoming the problem, the prospect of a dispute hanging over the project can strain the relationships between the parties and challenge their ability to work cooperatively to achieve the project’s objectives.
Importance of Adopting the Most Appropriate Contracting Model
Challenges with bridge projects may lead to cost time and cost overruns, making it critical to select a delivery model that can adequately deal with these issues whilst allowing the project to proceed. Where risks cannot be easily identified, or are unknown at the time of contracting, a contract should explicitly set out who bears the risks and how they will be managed should they arise during the project’s lifecycle.
Dispute Resolution Considerations
Importantly, parties should select a simple and practical dispute resolution process, which is often forgotten in the euphoria of a successful tender. The efficient and timely address of disputes can reduce the propensity for delays and cost overruns on projects.
Parties may consider staged escalation of dispute resolution processes that provide a forum to resolve the matter prior to litigation. Further, parties are open to specify that certain disputes or issues must be referred to dispute resolution processes, ensuring matters are addressed in the most appropriate forum.
Lamont Project & Construction Lawyers
We have the industry knowledge and experience to assist both Principals and Contractors in all major bridge projects, their unique challenges and implementing contractual frameworks which best align with project objectives. If you have any questions about any matters raised in the above article or the forthcoming series as it relates to your specific circumstances, please contact Lamont Project & Construction Lawyers.
The content of this article is for information purposes only; it does not discuss every important topic or matter of law, and it is not to be relied upon as legal advice. Specialist advice should be sought regarding your specific circumstances.
Contact: Peter Lamont or Kristopher London
Email: peter@lpclawyers.com or kris@lpclawyers.com
Phone: (07) 3248 8500
Address: Suite 1, Level 1, 349 Coronation Drive, Milton Qld 4064
Postal Address: PO Box 1133, Milton Qld 4064