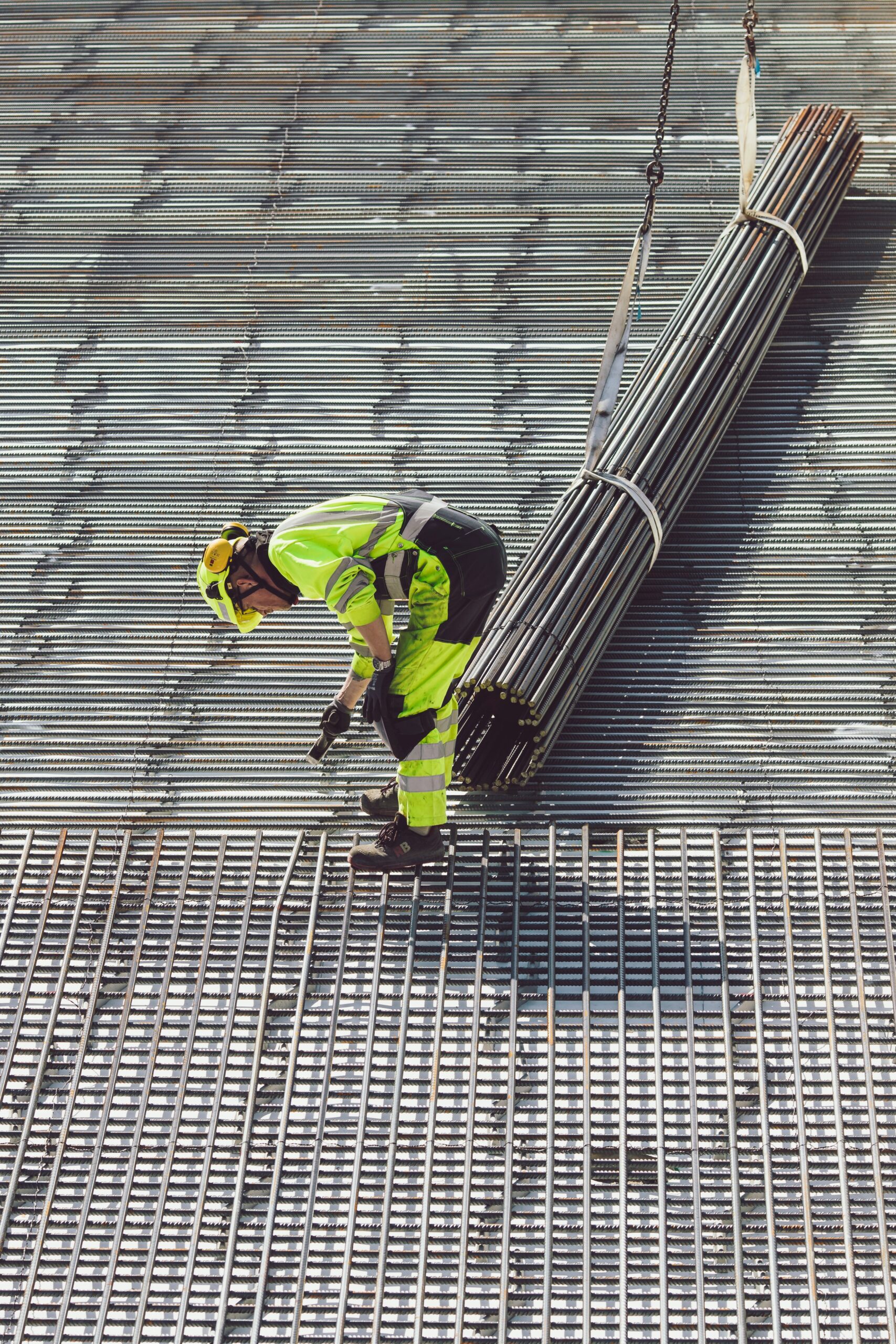
Construction contracts are the primary tool for allocating known and unknown risks between principals and contractors; however, COVID-19 has emphasised the tendency for a disproportionate allocation of risk on contractors for procurement. This has resulted in contractors experiencing additional financial burdens due to unforeseen costs not accounted for during bidding. It is imperative for contractors to consider the different approaches taken to risk allocation in all contracting models so that procurement risk is properly managed.
Project Procurement
In the construction industry, project procurement involves sourcing and securing all materials needed to complete the project with efficiency and to an acceptable quality. Procurement management is an essential aspect to mitigating risk and maximise the efficiency of the project. When choosing a procurement approach that is best suited for your project, critical factors include cost/budget, material quality, project-specification requirements, time, and procurement risks.
Project procurement risk refers to circumstances where there is a failure to purchase or problem sourcing the required materials, services, or equipment required for your project, which may lead to escalated project costs and/or missed deadlines, milestones, or deliverables under your contract. Contractors can mitigate risk of delays by having awareness of contract completion dates and procuring materials based on estimate delivery dates and current market rates.
Pre-pandemic many contractors assumed procurement risks and now face significant losses. Contractors to current projects who are dealing with procurement difficulties flowing from the pandemics impact on supply chains, should closely review how risk is allocated in their contracts when determining what, if any, contractual relief is available.
Risk Allocation
As new contractual agreements are entered into post-pandemic, there is an increased need for consideration of balancing principals’ desire for cost certainty with contractors’ concerns surrounding the future unpredictability of pandemic risks and the impossibility of pricing these risks. When assessing which party is best suited for preventing the known risk and which party is best suited to manage the consequences of the unknown, contractors should consider whether they have the capacity and experience to manage the identified risks and the financial capacity to withstand unknown risks.
For contractors, proper risk allocation is an essential mechanism for mitigating financial loss and delay. It allows both parties to collaboratively identify where possible risks may arise and account for what aspects of the project may be more susceptible to cost overruns.
Where the procurement of materials and equipment sits with contractors, when and how much to buy should be the primary consideration. In other words, contractors’ minds should turn to when materials and equipment are required, how much it will cost, how it is accounted for in the design/contract price, and whether the supply of particular materials is more likely to be impacted by market forces.
At a high-level, procurement of materials and equipment can be contractually managed by:
- Allocating provision for cost overruns above an agreed upon percentage;
- Inclusion of a cost escalation clause for identified materials that may be subject to significant increase due to market forces;
- Seek to pass the risk back to the principal by having them procure key materials;
- Contingency for materials and equipment priced via market analysis of materials and equipment required.
Where principals and contractors work collaboratively to allocate risk with a focus on maintaining the viability of the project and the efficient completion of the project, the pandemic related risks will be minimised.
Main Take-aways
In the post-pandemic market, contractors and principals are approaching the procurement of materials to accommodate for uncertainty by sharing the risk of procurement or considering the viability in diversifying suppliers.
Contractors most certainly benefit from a more defined due diligence over the entire supply chain (material and equipment suppliers) of their project by assessing key suppliers in light of identified project risks and addressing potential future supply chain disruptions, to develop contingency plans that consider:
- Whether domestic suppliers are capable of, and have the capacity to, provide insurance against international market fluctuations;
- Alternative supply options located in multiple jurisdictions, to account for possible cost increases; or
- Advanced purchasing and storage of materials, equipment and additional parts.
Contractors with established supplier diversity and contingency plans (including contractual safeguards) will hold flexible options to counter the current procurement cost increases and uncertainty.
Lamont Project & Construction Lawyers
Lamont Project & Construction Lawyers are well versed in traditional contracting models and are highly competent in process from procurement support through to project completion with the ability to provide holistic advice across a project’s lifecycle. As we enter the post-pandemic era, our experience enables us to collaborate with clients to ensure the contracting processes are tailored to suite specific requirements of the project and deliver optimal results.
If you have any questions about any matters raised in the above article or the forthcoming series as it relates to your specific circumstances, please contact Lamont Project & Construction Lawyers.
The content of this article is for information purposes only; it does not discuss every important topic or matter of law, and it is not to be relied upon as legal advice. Specialist advice should be sought regarding your specific circumstances.
Contact: Peter Lamont or Quinn Hironaka
Email: peter@lpclawyers.com or quinn@lpclawyers.com
Phone: (07) 3248 8500
Address: Suite 1, Level 1, 349 Coronation Drive, Milton Qld 4064
Postal Address: PO Box 1133, Milton Qld 4064